Personal Productivity
Looking For The Perfect Productivity? Stop Putting Out Fires
AUTHOR: Francisco Sáez“Prevention is better than cure.” ~ Popular saying
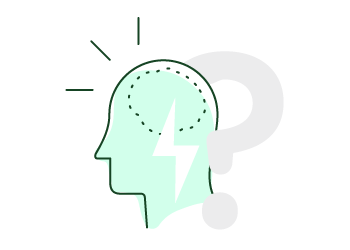
Of all the activities you do, which one do you consider the most important? Solving problems? Fixing errors? Taking new projects?
Unfortunately, we spend too much time solving problems and fixing errors that have been generated by some things that we haven’t done too well. And this means that we cannot have the necessary time to face new and interesting challenges… and that our productivity sucks.
In industrial environments, preventive maintenance goal is to achieve an ideal production system, preventing failure of equipments and facilities. If there are no faults or defects, or stops in the production lines, productivity would be perfect. This can be achieved by systematic inspections, and detecting and fixing problems before they become serious incidents.
In contrast to preventive maintenance, corrective maintenance is to repair a system failure or damage when it occurs, so the system can continue to operate as normal. When there is a failure, production stops and, therefore, productivity decreases.
When your car breaks down and you have to bring it to the workshop to get it working again, you’re doing corrective maintenance. When, every 15,000 km. or so, you change the oil in your car to prevent engine failure, you’re doing preventive maintenance.
In the field of personal productivity, the problem is similar. Many times we are fighting small crises and dedicating our time solely to solve a problem that has just emerged in order to be able to continue our work. We solve it—apparently—and we do not realize that this type of problem will arise again and will steal our time on many other occasions.
Solving a problem is not just fixing it. The corrective action must be followed by a thorough analysis of the cause of the problem. And, surely, from this analysis a set of new preventive actions need to be implemented so that the problem won’t happen again.
Yes, it seems a lot of work for a problem that appears from time to time, but read on…
Stop the lines!
Many years ago, in the Toyota manufacturing plants (and the rest of the auto industry), stopping a production line was something that only the head of the plant could make—the cost of stopping a line is very high, tens of thousands of dollars per minute!
When Taiichi Ohno introduced the idea that any line worker should have the authority and responsibility to stop production when a problem appears, many thought it was crazy. The idea was to give immediate and absolute priority to the problem, and only restart the line when the problem was resolved.
After restarting the line, a team of experienced people should conduct a root-cause analysis of the problem to understand what happened and try to fix the real problem.
Some managers heeded him and others not. Those who heeded saw how the productivity of their lines diminished because of all the stops that were taking place to deal with the problems that arose. However, over time, managers who allowed their workers to stop the line to solve problems, began to see that the lines were stopping less and less frequently.
Defect prevention was generating a continuous improvement in the quality of the process, and the results were soon better than those lines that had not followed the policy of Taiichi Ohno.
Conclusion
If you want to improve your productivity and spend less time putting out fires, use defect prevention in your problem solving:
- Detect the problem.
- Stop what you’re doing.
- Fix the problem.
- Investigate the root cause of the problem.
- Implement a real solution.
Steps 2 and 3 facilitate that problem solving becomes a habit and not just something you put off until you find a better time. Step 4 gives you the opportunity to understand how your processes really work. Step 5 makes you more productive and improves the quality of the result of your work.
Routines and repetitive tasks are the points where you anchor the preventive maintenance of your personal productivity. If you practice GTD, when you perform The Weekly Review and you revisit the actions and projects completed the previous week, seriously consider the possibility of completely closing the seemingly solved problems, and reduce the risk of their recurrence.
2 comments
I would add:
6. Share the defect reason and the correction.
Because fixing alone is not enough !
I would add:
6. Share the defect reason and the correction.
Because fixing alone is not enough !
Hi Philippe, that's a good point.
Thanks!
Hi Philippe, that's a good point.
Thanks!